I’m starting to lose count of the number of Mining industry customers who (over many years and many iterations/versions of SAP) call me to review their Cost Model!
Is it because the mining companies rely on the advice of implementors who have little or no Mining knowledge? I don’t know, but it seems to be the same story every time.
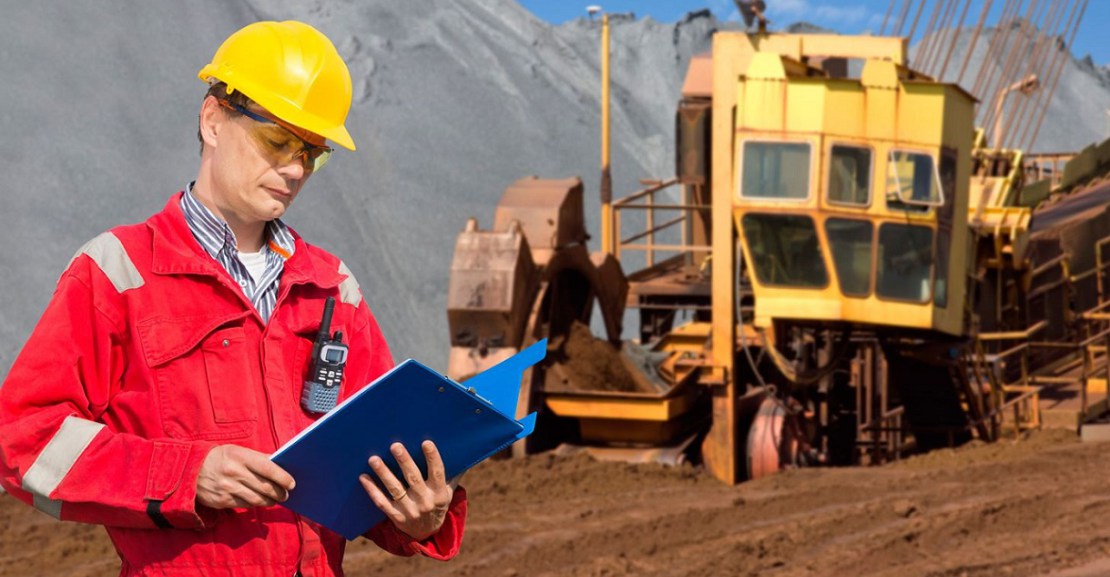
The typical comments relayed to me by mine management include:
- It is not working, so we have started to track our SAP costs model offline
- After all the allocations, we don’t understand our costs!
- It is too complicated, and we don’t understand it
- I’m getting costs allocated to me which I don’t even control!
The truth is that most managers are happy to be measured on their SAP cost model management performance, and (in my view) implementors have an obligation to make it as simple for them to do their job as possible. A design which satisfies the financial accounting requirements but forgets the real cost collectors leads to a heightened amount of confusion and concern for the average time-poor manager.
That SAP Cost Model can broadly be described as the cost collection, cost allocation and cost object set up in SAP which ensures that all the business cost reporting and analysis requirements are met. There are many requirements which need consideration, and many of those are satisfied within SAP by standard or industry-specific functionality.
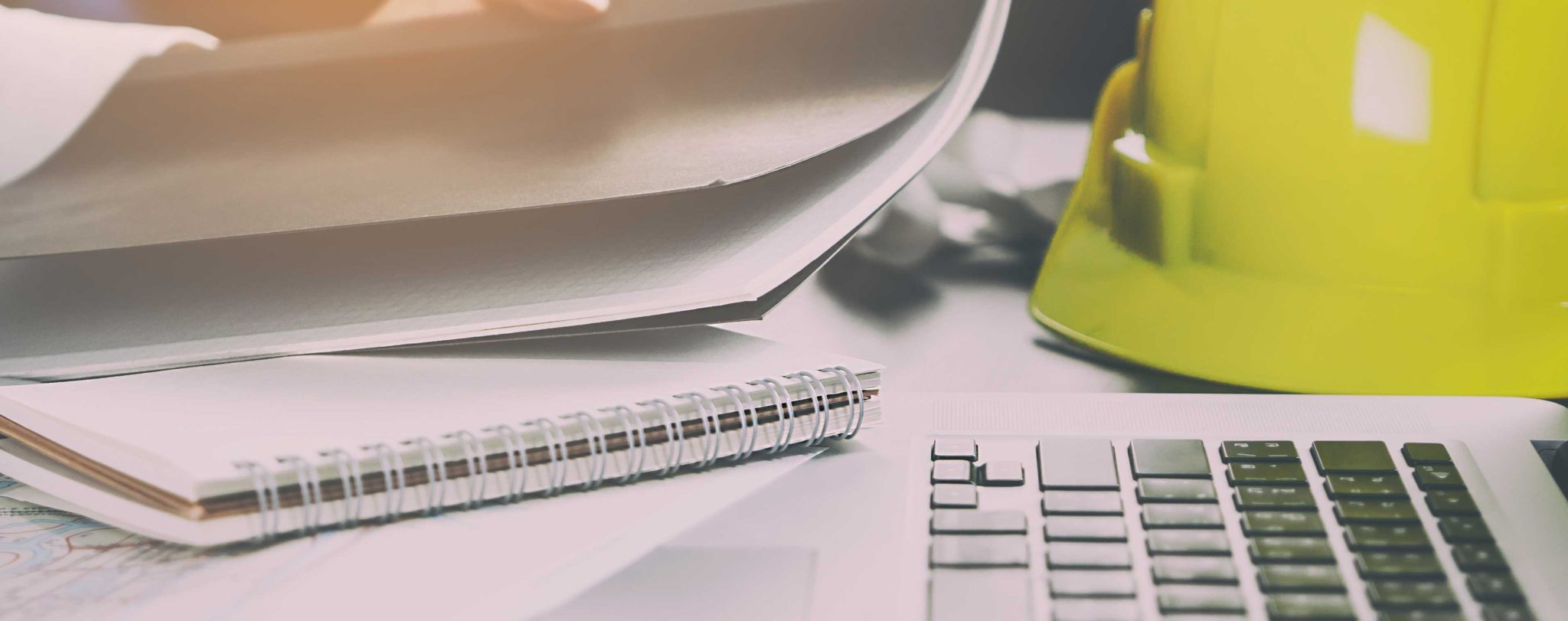
The concepts often discussed include:
- Cost collection objects (Work Orders, Cost Centres, WBS/projects, Orders, etc)
- Settlement of costs from intermediate cost collectors
- Cost allocations or assessments (allocations)
- Joint venture costing
- Inventory valuation (inventory roll)
- Internal business (which is an inherent feature(and confusion) in SAP)
For a SAP implementor who is presented with a functionally rich SAP, there are many who (whether consciously or sub-consciously) think of themselves instead of their client by either:
- extending SAP usage irrespective of the workability of the business process,
- extending their own knowledge of SAP (great, I’ve made SAP do a backflip!), or
- adding additional scope to build a Ferrari rather than a Ford (which is what is required).
Creating a SAP Cost Model which takes days on a whiteboard to explain (purely because the system can do it) may be a great demonstration of SAP capability, but it doesn’t help the customer at 2am during the next plant shutdown, when the pressure is running high.
PM Eleven
At PM Eleven, as Mining specialists who have worked in line-roles on mine sites, we know the rigours of being time-poor and shift-based!
The mining workforce is often a wide range of skilled and semi-skilled personnel, so the SAP Cost Model has got to be able to traverse up, down and across the organisation and everyone
There are some key rules we follow at PM Eleven when we advise our clients about the SAP Cost Model:
- It must be built primarily to reflect the mining “process” (whether that is gold, copper, zinc, lithium, diamonds, mineral sands, whatever),
- It must have
clear understanding of the responsibility assignment, - It must be easy to understand (<30 min conversation), and
- It must be underpinned by governed data structures, but it must also be flexible (for the unexpected!)
And, most importantly, design a “practical” rather than a “theoretical” solution
everytime .
Final Thoughts
Are you a CFO, Maintenance Manager or Operations Manager at a Mining Operation?, Do you want to understand more about SAP Cost Model?, feel free to contact the PM Eleven team for a free discussion with our Mining experts.
If you want to join us on this journey and see where it takes us – please Contact Us or Follow our LinkedIn Page.
Mark Cooper
CEO – PM Eleven